LASER WELDING – THE KBB LASER WELDING PLANT
As the European market leader for laser-welded absorbers KBB offers the best quality characteristics:
- Full-automatic, CNC-controlled welding unit
- Highly precise focusing of the laser beam and performance increase
- 100% full-automatic pressure test in a closed cabin
- Automatic production data acquisition and thereby Traceability of the products
- The resistance and longevity of the welding seam with around 25,000 welding spots per absorber is proven through accelerated ageing tests!
The Process
A pulsed laser melts open small areas of pipe and metal, and the meltings mix. The aimed and precisely dosed laser beam only heats the absorber at the welding dot, so that the heat-affected zone is kept very small. Therefore, material stress and warping remain at a low level. That way, about 1,000 welding dots per one meter pipe ensure a permanently strong connection and an outstanding heat transfer.
A technology with lots of advantages
- Excellent operating characteristics:
Fusion welded joints are extremely strong and temperature-resistant. The outstanding heat transfer is just as good as the one of a soldered absorber.* - Flexible design and precise performance:
Pipes and absorber metal can be almost 100% connected. Upon request, the KBB process attaches pipe bends and manifolds. - Consistent quality:
The laser welding technology enables high process stability. - Versatility:
Different material pairs are possible, especially aluminium and copper. - Aesthetics:
The welding is done on the back of the absorbers, so the highly selective absorber surface remains almost intact. - Environmentally friendly:
Our products are completely free from poisonous filler materials and recyclable.
A Technology with a Future
Since good things can always be further improved, we use a new, much more energy efficient laser source in our fourth, newly built laser welding plant. It significantly reduces the energy consumption per welded absorber.
* Test Report ISFH 65-04/V 01/17/2005
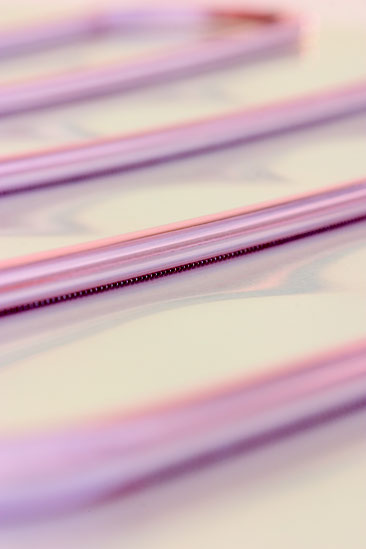
Specification and Data
Absorber Type | Full-surface absorber |
Pipe Layout | Harp or meander |
Absorber Length | 1,000 – 3,000 mm |
Absorber Width | 500 – 1,300 mm |
Sheet Thickness | 0,2 – 0,8 mm |
Materials | Al/Cu, Cu/Cu, Al/Al |
Coating | All standard ones |
Outside Diameter of the Pipes |
8 – 35 mm |
Necessary Space between Pipe and Sheet Edge | ≥ 20 mm |
Clear Distance between the Pipes |
≥ 70 mm |
Pipe Run | Freely programmable |